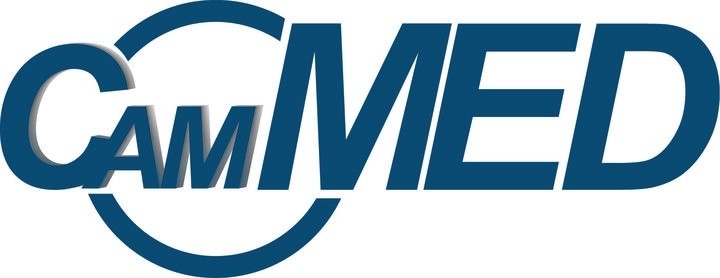
Two years ago, Cam Med Inc. was a Finalist in the 2018 M2D2 $200K Challenge. Since then, Cam Med’s cofounders, CEO Larry Alberts and CTO Zhifei Ge have been the very model of “seize every opportunity” startup leaders, taking advantage of virtually every chance for learning, mentoring, financing, and networking that’s come their way. The result has been a steady upward trajectory for their innovation: the Evopump, a wearable on-body delivery system for injectable drugs.
Here’s an update from Larry on what’s been happening at Cam Med—and what’s on the horizon.
We’re all about innovation here, so let’s start with yours. Introduce us again to the Evopump.
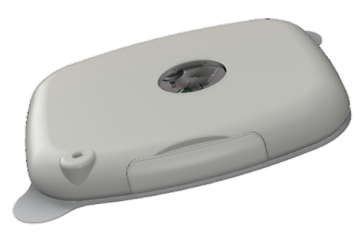
The Evopump is a highly flexible platform technology for delivering injectable drugs into subcutaneous tissue as a wearable on-body delivery system (OBDS). Our platform technology changes the OBDS paradigm. To gain pharmaceutical companies’ acceptance of OBDS designs, developers of these systems have taken as their primary objective to minimize the disruption to the fill-finish and sterilization processes of the drugs made by their potential pharmaceutical partners. The principal means to achieve this has been to start with the original drug primary container (a vial or cartridge), and then design a mechanical actuation system around the container. The consequent result is that these devices generally appear similar: a bulky, hard plastic shell whose shape is dictated by the size and shape of the vial.
Unfortunately, the patient experience is a secondary consideration. A common priority for patients—across therapeutic areas, demographics, and specific conditions—is a desire to return to “normal” life as readily as possible, yet these devices are highly intrusive into daily life. Their preparation, application and use processes are numerous and complicated, leading to poor acceptance and compliance.
The design of Cam Med’s Evopump platform starts with the patient experience, while also meeting the requirement of minimizing disruption to pharma’s fill-finish and sterilization processes. Additionally, the Evopump platform enables other unique attributes critical to commercial success and a broadening of the opportunity for pharmaceutical companies: an unparalleled low-cost structure, matching that of an auto-injector, and the potential to co-deliver multiple medications automatically from a single device.
What sets Evopump apart in this space?
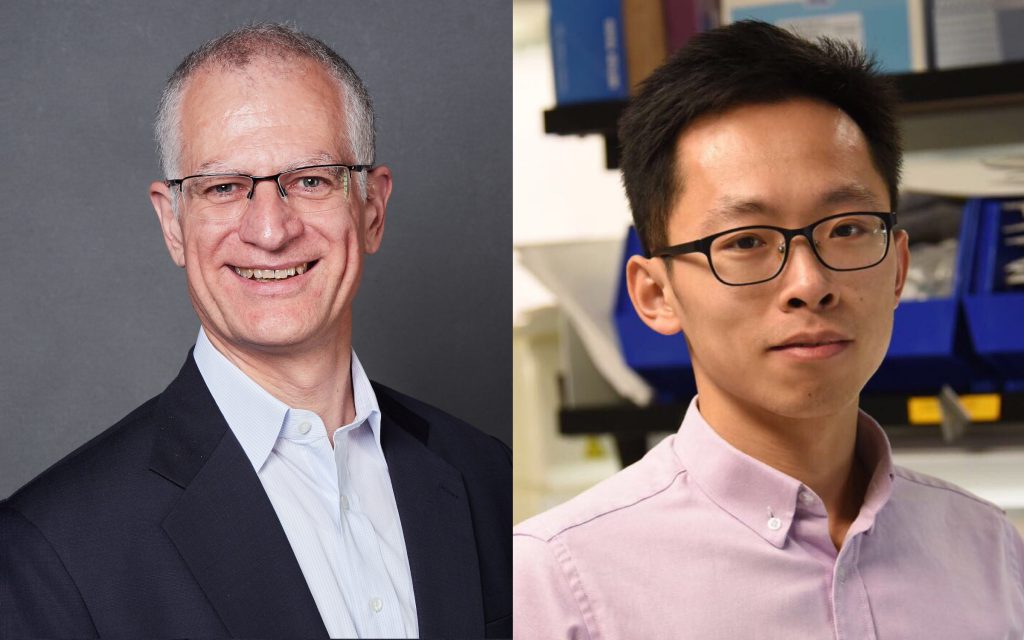
Evopump’s design is fundamentally different from other OBDS technologies in several critical respects. First, rather than requiring the patient to wear the bulky primary container, the Evopump places the primary container in a removable applicator. The applicator, when activated by the user, transfers medication into a disposable patch. Then, in one single step, the patient holds the applicator against the body and presses a button, upon which the applicator adheres the patch to the user’s skin, inserts a soft cannula for medication delivery under the skin, and detaches itself for disposal, leaving behind on the skin an ultra-thin patch which holds and delivers the medication.
The second critical difference is that rather than having a single large electromechanical reservoir and drive mechanism, the Evopump is comprised of an array of miniature micropumps. These micropumps operate based on electrochemically-evolved gas pressure, which is used to deflect a set of membranes inside the micropump that displaces medication. This geometry enables the overall device to be ultra-thin in depth, the most critical dimension from users’ perspectives.
The design of Cam Med’s Evopump platform starts with the patient experience.
Additionally, the platform design is modular, with an ability to change drug volume capacity easily by adding or removing reservoirs, and it enables a highly simplified and low-cost manufacturing process, whereby the device is fabricated from inexpensive formed plastics which are assembled and thermally-bonded in purely vertical movements which also lend themselves to high throughput roll-to-roll manufacturing processes. Control electronics are integrated into a reusable module which is inserted and removed via a simple USB-type connection, reducing disposable waste and further lowering unit cost to the level of an auto-injector yet having the ease-of-use and patient appeal of a highly discreet OBDS.
Lastly, with the Evopump having multiple reservoirs, it has the unique potential to deliver multiple medications from a single device, providing the flexibility to co-administer therapeutically-relevant combinations, such as anti-nausea medication with an oncology drug, insulin with glucagon or with amylin for diabetes, or an uptake enhancer to accelerate absorption of a medication, providing pharma partners with further commercial opportunity by reducing side-effects and improving efficacy of their medications.
What’s happened with Cam Med since the 2018 $200K Challenge?
We’ve made great strides since being an M2D2 finalist, in terms of funding, our team, developing the technology, and establishing partnerships.
We closed a Seed funding round, which includes a mix of financial and strategic investors, and have also received significant resource commitments from JDRF International and Analog Devices. This has enabled us to expand our team, for example, adding a Chief Innovation Officer with three decades of experience in leading-edge design as well as a Chief Commercial Officer who has led alliance management at one of the most successful OBDS firms.
Early in March, our pump’s electrochemical engines were flown up to the International Space Station, where experiments are about to begin that will demonstrate the robustness of our core technology.
We also were invited into JLABS and have benefited greatly from that engagement. We initiated our first co-development collaboration with a major pharmaceutical firm around 18 months ago, and that’s going very well. After completing a proof-of-concept prototype last year, we’ve now been working together to get the device “ready for prime time.” We’re also energized by two other global pharmaceutical companies very interested in our technology, and we’re gearing up to launch an animal study with one of them this summer.
We were fortunate to have been able to complete our first human factors study just before Massachusetts “shut down” as a result of the pandemic. The feedback from patients and providers has been both very positive as well as informative to our design. We were able to down-select to a preferred applicator design, and we got very strong confirmation of the appeal of our ultra-thin patch design and the overall simplicity of use.
I’m also excited to see our technology in the International Space Station as we speak. We were awarded the CASIS/Boeing prize a number of years ago, and early in March, our pump’s electrochemical engines were flown up to the ISS, where experiments are about to begin that will demonstrate the robustness of our core technology.
Tell us about Cam Med’s experience as an M2D2 resident company.
We came to M2D2 at the beginning of 2017. There were two catalysts for this. One of our advisors, Francis Lai, is Professor Emeritus at UML’s Plastics Engineering Department. We sponsored research under him, and this eventually led to one of his students starting as an intern with us. That student is now one of our key engineers. We also were the lucky beneficiary of an offer of discounted rent at M2D2 as a result of being a winner at a competition called the Diabetes Innovation Challenge. This was an offer too good to pass up, so we moved from our initial lab in Allston to the Wannalancit building in Lowell, and we’re now in our fourth year here.
Being an M2D2 resident has helped us in many respects. Mary Ann Picard and the team have always been supportive of helping us secure what we need. We were the beneficiary of a subsidized loan from the Lowell Development & Finance Corp’s Launch in Lowell Program, which has been very helpful from a working capital standpoint, funding gaps between our expenditures and receipt of milestone payments. We’ve taken advantage of the equipment and facilities available, from running UPLC tests of material compatibility over at 110 Canal Street to validating gamma sterilization using radiation equipment from the university. We’ve hired a number of UML students as coop interns. We’ve had investors and potential partners from around the world visit us and they are always impressed by the facilities.
Flying aboard the ISS is hard to top, but what’s next for Cam Med?
The next 12 months will be an exciting period for us. In three months, we’ll have completed a set of prototypes showing the full capabilities of our technology platform: precision delivery (e.g., for insulin), bolus delivery (e.g., for viscous biologics), and multi-drug delivery (for co-administration of medications). Pandemic permitting, we’re scheduled to have demonstration sessions with a number of pharma companies around the world this summer.
We’re also excited about a rebranding initiative we’ve been pursuing, along with a new website that will do a far better job at showcasing our technology and its capability and impact on users—more on those to come soon!
Please join us in wishing Larry and his team every future success. If you’d like to learn more about becoming an M2D2 Resident Company, email m2d2@uml.edu.
Pingback: MedicalMetrics ISO Certifications | Resident Companies | M2D2 BlogM2D2